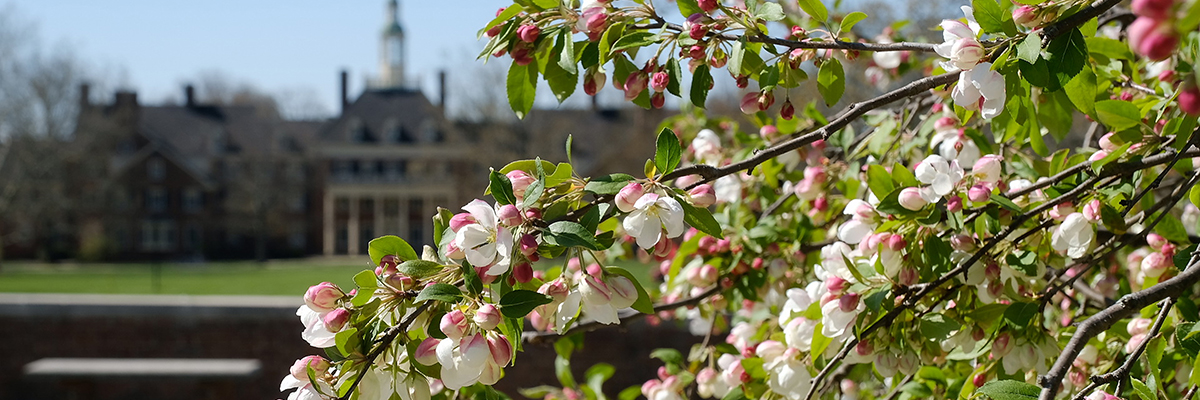
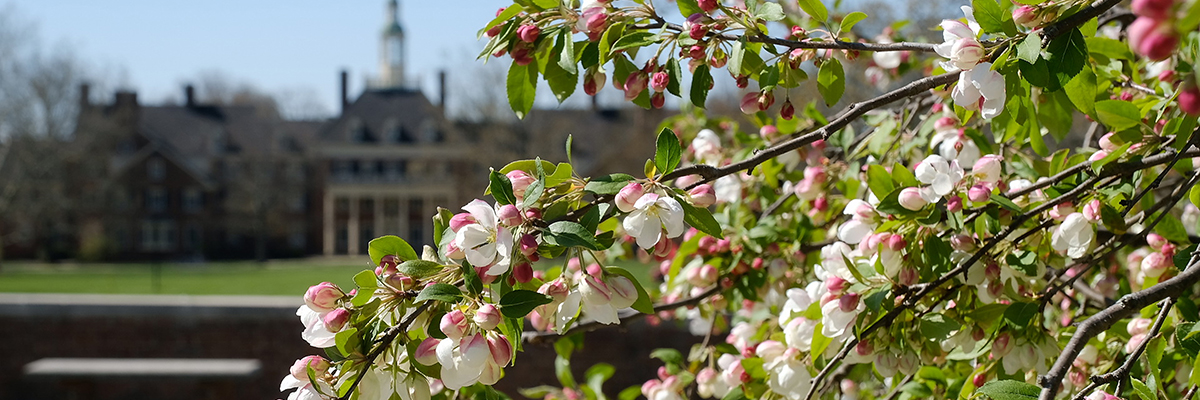
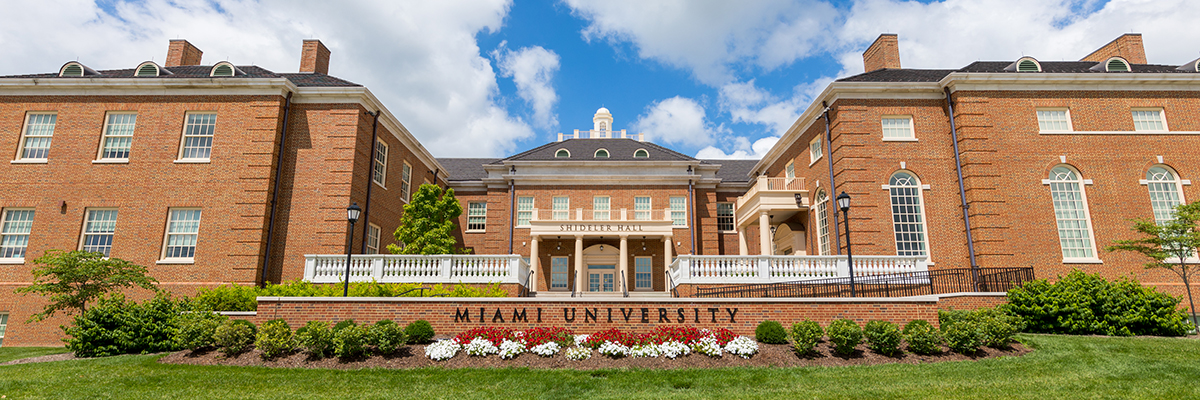
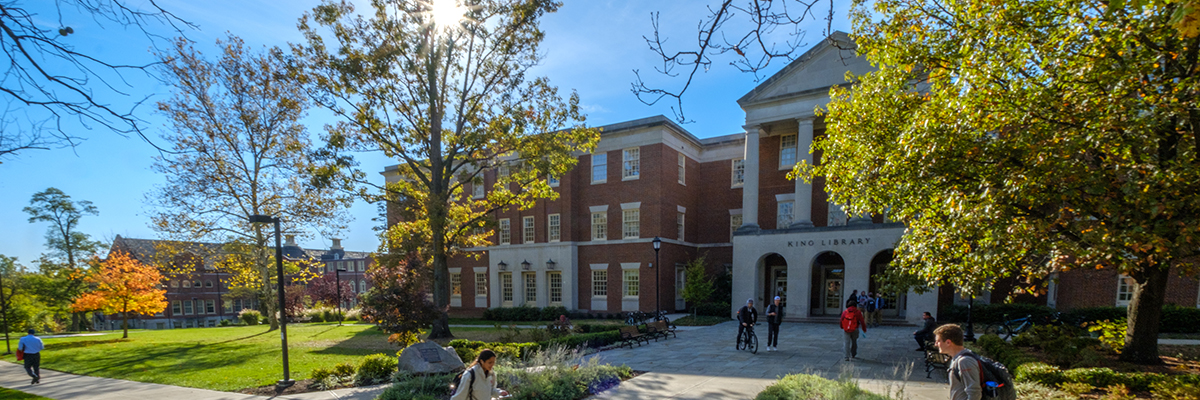
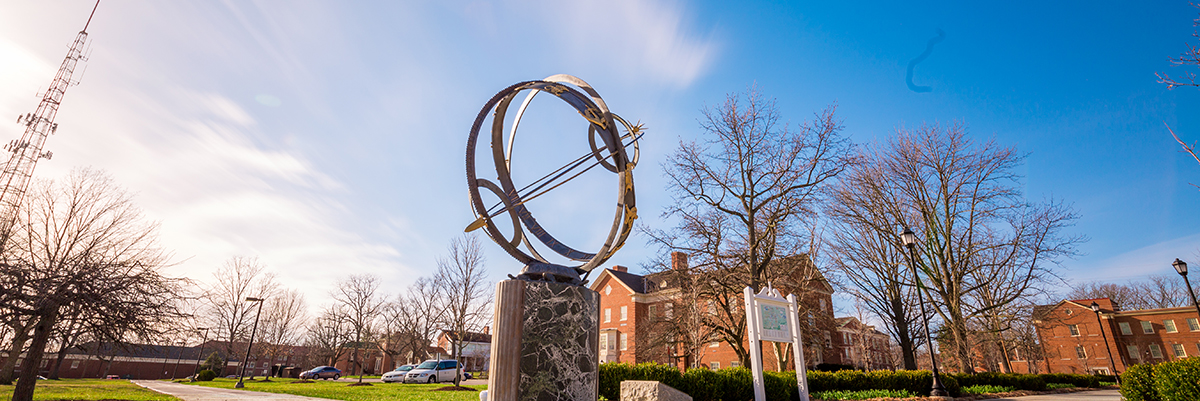
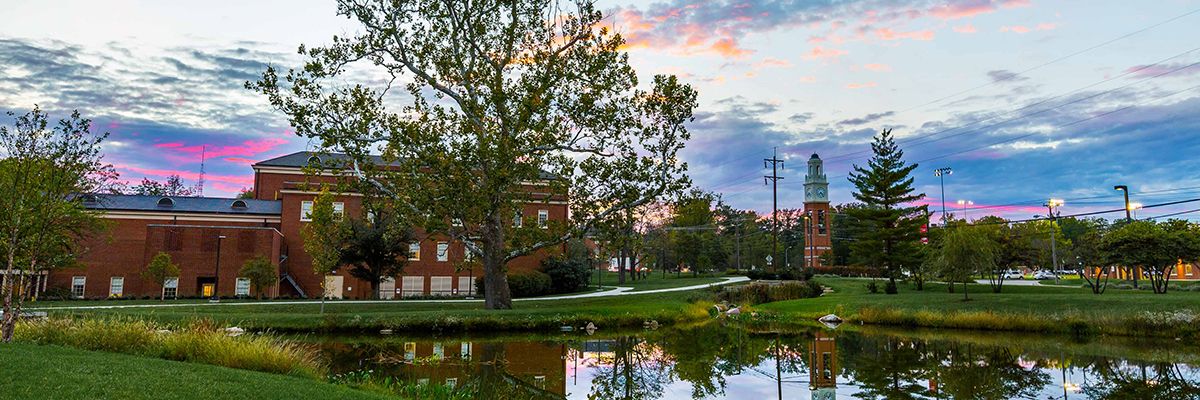
The Finance and Business Services Division is the steward of Miami University's human, fiscal and physical resources. Working largely behind the scenes, the staff serves internal and external constituencies in a manner that consistently supports the achievement of our vision of making Miami University the leader in the nation among public universities having a primary emphasis on undergraduate education and also having significant graduate and research programs.
Working at Miami
Lean Initiative
Lean is a process that Miami uses to improve quality, responsiveness, and productivity, and reduce costs by analyzing the work and finding ways to improve it. Suggestions for new Lean projects are welcomed and encouraged. Please submit your ideas for continuous improvement through MyCard (login required).
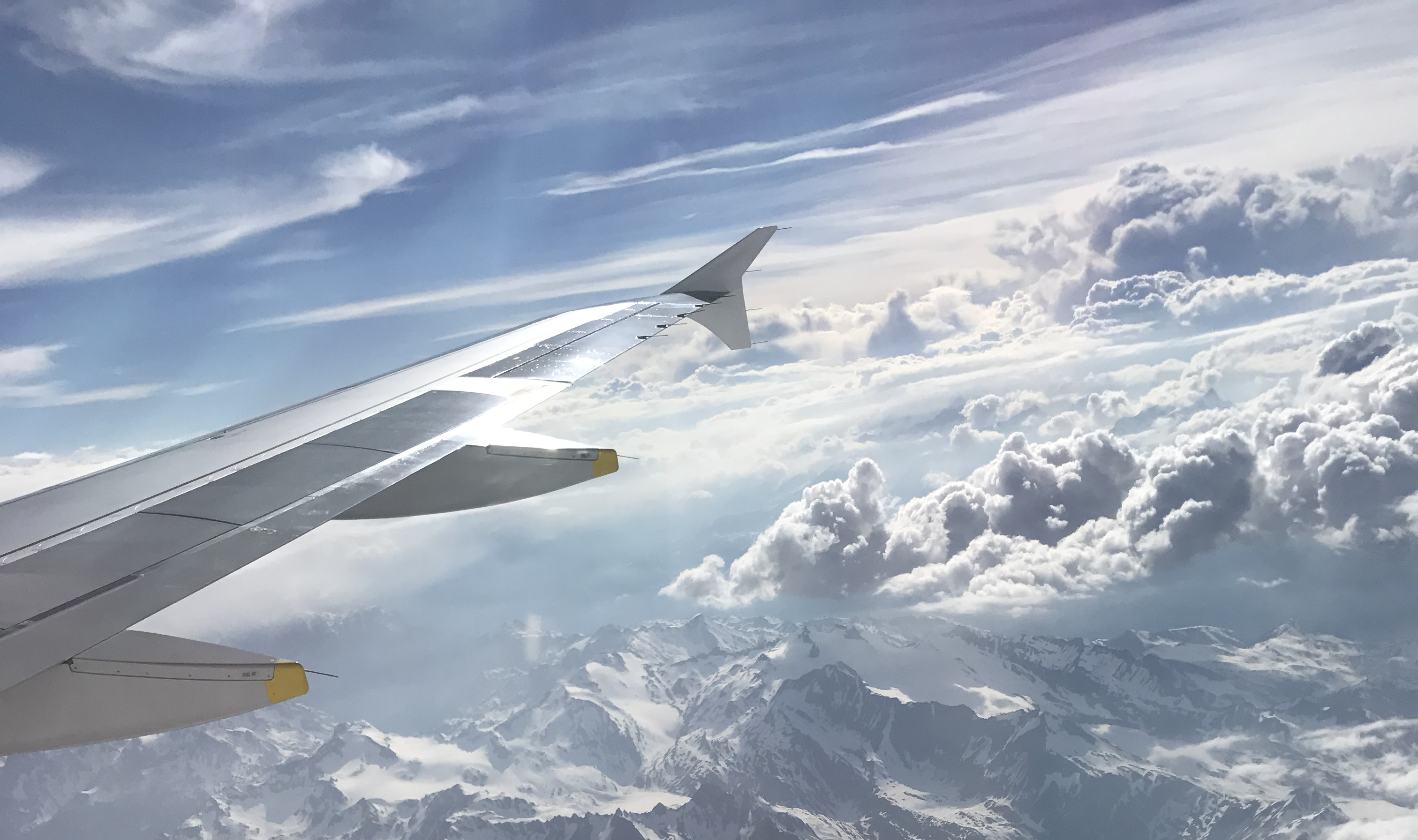
Traveling?
For all your business travel needs, use Miami's preferred travel provider, Options Travel.