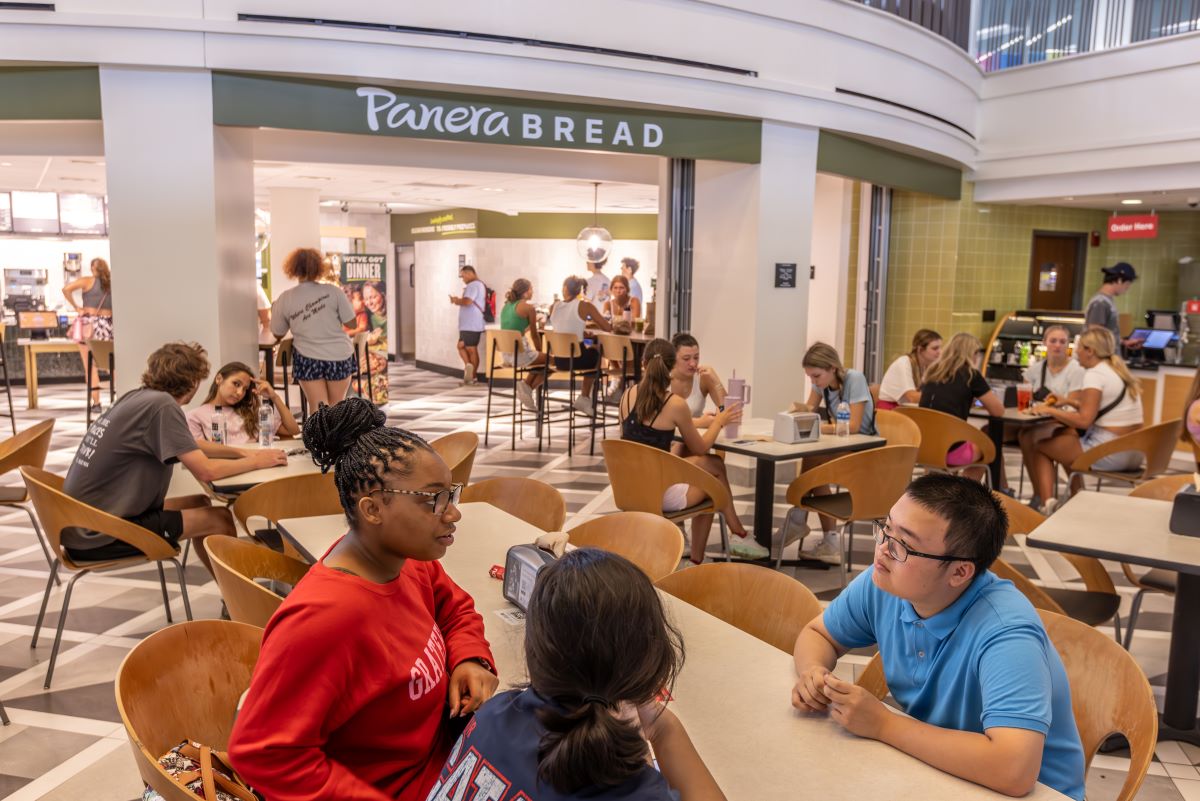

Finance and Business Services
The Finance and Business Services Division manages Miami University's resources to support its goal of becoming a leading public university with a strong focus on undergraduate education and notable graduate and research programs.
Business Services
Business services encompass a broad range of professional and operational support designed to help Miami operate efficiently and effectively. These services are crucial for Miami to streamline operations, enhance productivity, and focus on core functions.
Campus Experiences
Campus experiences are essential for building a holistic educational experience, preparing students for their future careers, and creating lasting memories and connections.

Finance and Business Services
218 Roudebush Hall501 E. High St.
Oxford, OH 45056 vpfinancebusiness@MiamiOH.edu 513-529-6110